The Next Shift: India’s Manufacturing Readiness Post Covid-19 Crisis
Change is buffeting the industrial manufacturing industry comprising of the most disruptive innovations that would address the customer’s pain point. However, there is no one-size fits-all strategy that suits all industries. A clear understanding on the trends would enable a successful transition from traditional manufacturing into the Industry 4.0. The first step for transitioning is the development of a comprehensive strategic road-map that carefully evaluates the end-to-end process of manufacturing value chain, also the cost and benefits associated with each step. The map should chart out few of the technology and design trends.
Technology Trends –
While, Industrial Internet of Things (IIoT) builds on the capacity of accurate and consistent data capture and holds a potential for enabling predictive maintenance services, green manufacturing initiatives, production efficiency along with energy & design optimisation. Internet of Services (IoS) scrutinises on the new ways of value creation through Product-as-Service (PaaS) and delivering product blueprints, a way to retain the customer base. Manufacturers are striving to establish a direct association by offering value-added services and cultivate additional sources of revenue. Internet of Data (IoD) relates to the data deluge addressed through effective means of data transfer, mining & storage and processing in a digitally connected environment where huge volume of data is churned through IoT. Although, Cloud Computing isn’t a new concept it would now be utilised as a foundational technology in convergence with other advanced technologies like Blockchain, Artificial Intelligence and Augmented Reality. Automation and industrial robotics has taken a step-up in manufacturing. Industrial robots are grabbing the space due to the ongoing trend toward automation among manufacturers.
The post COVID-19 impact would witness a lot of in-house manufacturing taking place addressing few significant issues like:
- Efficient production with a near to “zero-defect” quality monitoring.
- Shortage of labour and balancing the supply-demand fiasco
- Planning uncertainties in supply chain and sales operations that lead to cash liquidity
- election of market with respect to demand and economic crisis
- Cost benefits looking at the distorted supply chain and reduced global trade corridors
Additive Manufacturing/3D printing enables manufacturers to produce prototypes and proof of concept designs, which simplifies and speeds the process helping to stamp out extra costs.
Design Thinking –
Though there are umpteen number of ways to nominate transformation linking to the digital economy, systematising the role of design would be a delightful network of experiences for both the customer and the enterprise. The contribution helps to craft a digital road-map by highlighting the gap between the existing manufacturing system, simultaneous ongoing transformation, and the interconnectedness of technology and design practices.
There is an immediate need within manufacturing to shift structurally from low value-added sectors to high value-added sectors. Hence to enable this transition along with spending on R&D, sectors would require adopting advanced digital technologies and build a connected ecosystem. The revolution under way would be around the real possibility of using all or most of the advanced technologies to achieve both the optimisation of production system and addressing the gap between manufacturing and digital spaces. Parallel to the availability of enabling technologies, the manufacturing system has evolved and been meshed with design thinking.
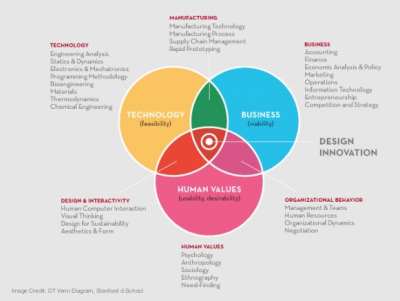
Digital adoption by India’s businesses has so far been uneven, but new digital business models could proliferate across most sectors. Also, the changing market dynamics is impacting the industrial manufacturing industry. Recent research by McKinsey indicates India’s core digital sectors accounted for about $170 billion that is 7% (in 2017–18) comprising of electronics manufacturing ($10 billion) and this could grow $100 billion to $130 billion in 2025. According to McKinsey estimates Government’s “Make in India” programme seeks to increase manufacturing’s share of GDP from about 16 percent to 25 percent by 2022, digital transformation is likely with the government taking measures on implementation of more digital technologies to allow supply-chain consolidation & analysis.
Adoption of Digitisation has a commendable score in manufacturing sector with maximum leaders and lesser laggards. (Sector median digitisation score is 45, highest being in ICT with 50). A recent Ernst & Young study indicates two-thirds of the manufacturing firms in India ranked big data and predictive analytics as the top investment priority in technology in the next 1-2 years. This was followed by sensors and IIoT along with cloud integrated platforms and robotic automation. The key factors driving digital manufacturing in India include predictive maintenance, connected supply chain, reduced energy consumption, production optimisation, lower price of sensors and high computing needs and connected customers. In addition, overall monitoring and visualisation is the most sought-after use case by manufacturing firms, followed by track and trace of the product across the value chain. However, unclear economic benefits from digital investments stand as a major constraint. Inefficient people skills on tech, analytics, cyber-security also remains a significant concern.
Pacing towards Industry 4.0 Post COVID-19 – Rebooting post lockdown would drive adoption of digital solutions/platforms. Disruption to the ecosystem both at the individual and at the industrial level will foster innovation taking on Industry 4.0. Nevertheless, some of the key enablers in driving Industry 4.0 would be the MSMEs playing a vital role for domestic & exports and contributing to the larger industries. As mentioned earlier, the ‘Black Swan’ crisis would require an agile supply chain obtained through a clear approach to risk and management the process visibility. One of the important aspects is the increased demand of telecom and eCommerce due to Covid-19 piloting the adoption of Automation, Connectivity Intelligence, Robotic Process Automation (RPA) and Internet of Things (IoT). While the Indian industry is in speculation at the current moment, a well-charted framework can mitigate disputes in line to the new normal.